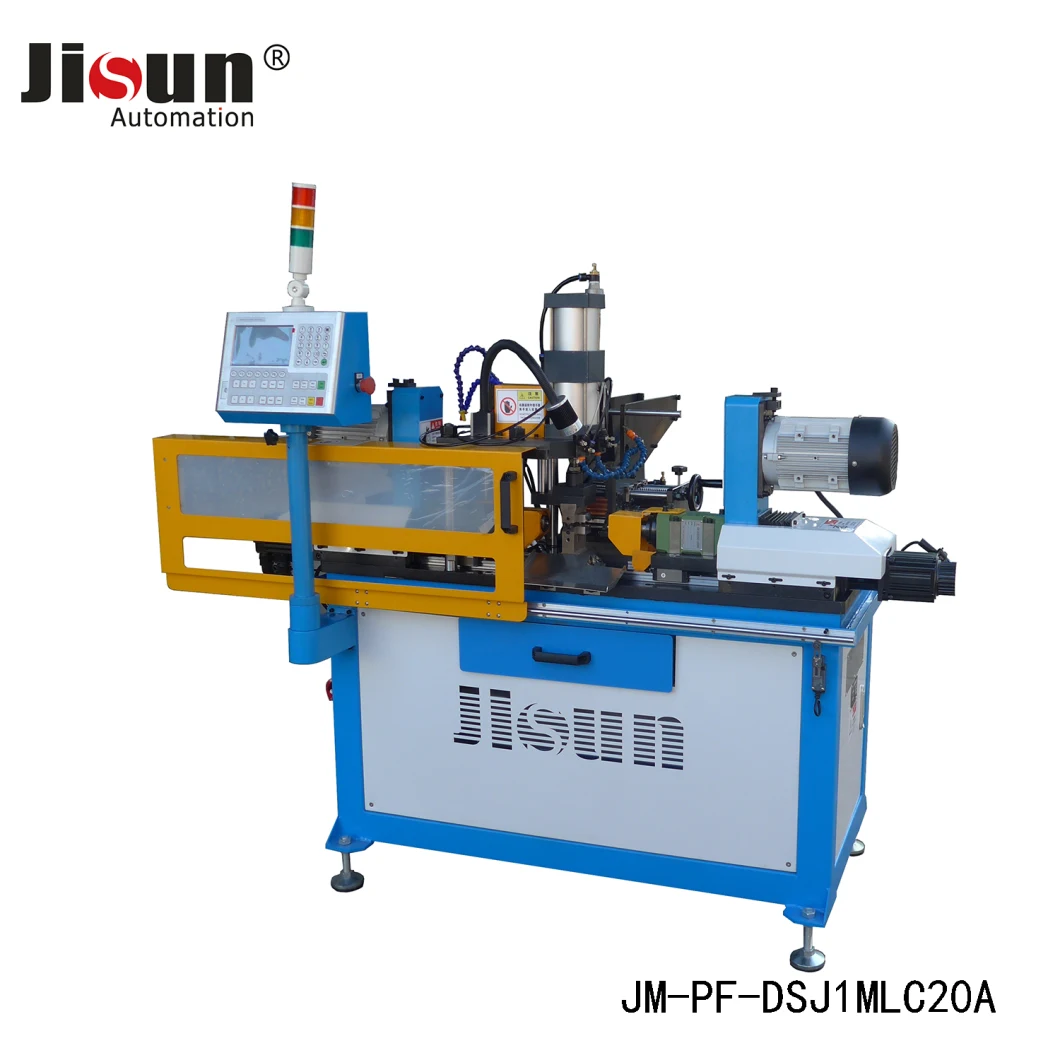
Use
This equipment is suitable for double-end forming processing (flaring, shrinking, shaping, chamfering, etc.) of copper pipe ends, and is mostly used for processing heat exchange products.
Features
- This equipment uses a numerical control system, which fully considers factors such as safety, convenient debugging and simple operation.
- The equipment control system has an automatic counting function, which can accurately count the processing quantity.
- The equipment has the function of tempo pause or continuous processing, and can be selected and changed.
- With automatic alarm function, when the device fails during operation, it will alarm.
- When changing products, mold replacement is convenient, fast and accurate positioning.
NO. | Parameter items | Content |
1 | Pipe diameter range | φ6.35-12.7mm |
2 | Pipe thickness range | 0.5-1.0mm |
3 | Pipe length range | 55-180mm |
4 | Work efficiency | 700-1000PCS/H |
5 | Number of stations | Main punch (2 cold punches + 1 rotation), secondary punch (1 spin) |
6 | Station moving method | servo |
7 | clamping method (cylinder bore * stroke) | Double force cylinder 100 * 50mm |
8 | Feed mode of punch (Servo power * stroke) | 1KW*75mm |
9 | Clip block unloading function | yes |
10 | Length error | ≤0.25mm |
11 | Coaxiality error | ≤0.08mm |
12 | Processing methods | Cold forging + spinning |
13 | Drive method | Servo / Pneumatic |
14 | Feeding method | Auto feeding |
15 | Operation method | Auto / Manual / Jog |
16 | Electric control mode | CNC system |
17 | air pressure | 0.5~0.8MPa |
18 | Rotating electric machine | Three phase380V/2.2kw*2 |
19 | Power mode | Three phase380V/50HZ |
20 | Overall dimensions (length X width X height) MM | 1600x800x1400 |
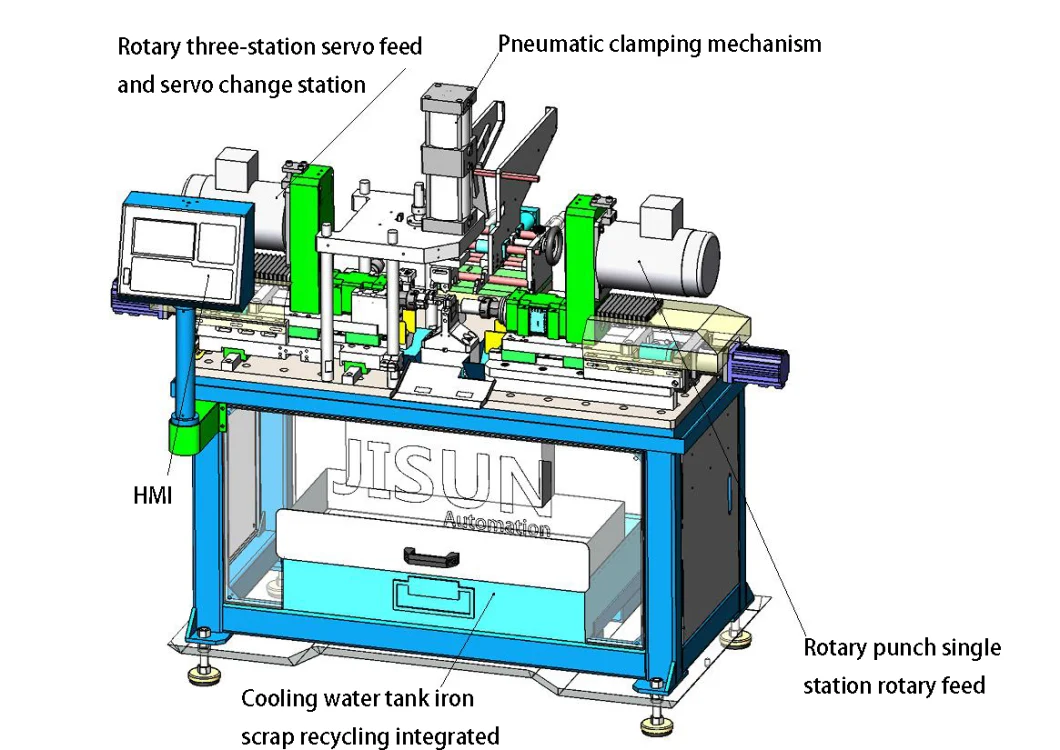
Equipment structure and system configuration
- Overview:The equipment consists of a frame, a power head, a feeding system, a servo system, a linear movement mechanism of the station, and an electronic control system.
- Frame: The fuselage is welded by profiles, and processed after vibration aging to ensure rigidity and accuracy of the mounting plane. It is equipped with four height-adjustable foot cups and safety protection doors;The parts of each part of the equipment are subjected to necessary surface treatments such as electroplating, blackening, quenching, carburizing, electrostatic spraying, etc. according to the actual working conditions and working environment to meet the components with sufficient strength and surface functions.
- Power Head:The maximum speed is 3000 rpm and it is driven by a timing belt. The dual-axis feed power is controlled by a servo motor and has 4 speed modes, which can be applied to the nozzle rotation molding processing (flaring, necking, chamfering, etc.)
- Feeding system:Using a special feeding mechanism, as long as the mold is replaced without screws, it can be connected lightly, which greatly shortens the installation time, and even the operator can quickly install it.
- Servo system: The servo feed consists of two sets of guide rails and a set of screw rods, which are composed of kinematic pairs, with high transmission speed and high precision.
- Station linear movement mechanism:The servo mode is used to drive the linear guide to move the mode during the conversion of the mold, and the rotation position is precisely positioned to achieve precise and rapid movement.
- Coloring:The main body of the device is blue (Jisun color number JS-SK-003), and warning signs are placed on the parts involved in personal safety.
- Electric control cabinet:Using the CNC system, the air switch adopts domestic high-quality air switch, Schneider button, and other main electrical components such as select switches and intermediate relays are all OMRON products. The control circuit is provided with overload protection function.
- The installation of the electrical components of the equipment complies with the relevant national regulations and has a reliable grounding device. The terminals, contactors and small air switches in the electrical box are installed in the VDE standard V-groove. Each electrical component is clearly marked. The electric control cabinet uses all-plastic combing cabinets with wire trunking for clear wire numbers; the control panel is clean and the subtitles on the signs are clear and easy to see.
- List of main accessories
NO. | Name | Quantity | Brand |
1 | CNC system | 1 set | JISUN |
2 | Pneumatic Components | 1 batch | AIRTAC |
3 | Leakage switch | 1 piece | CHINT |
4 | Boring head | 2 batch | HUNKUN |
5 | Rotating electric machine | 2 piece | GUANGZHOU MICROMOTOR |
6 | Servo motor | 3 batch | DELTA |
7 | Guide | 1 batch | TBI |
8 | Lead screw | 1 batch | TBI |
9 | Electromagnetic contactor | 2 set | TAIAN |
10 | Intermediate relay | 1 batch | OMRON |
11 | Transparent case fuse box | 1 piece | CHINT |
12 | Switching power supply | 1 piece | MV |
- Check the air / oil pressure and the condition of each fastener daily to ensure reliable use.
- Regularly lubricate moving parts and keep the equipment tidy.
- Clean the dust of the equipment regularly to avoid affecting the operation and product quality.
- The normal working time of the equipment is calculated from 8-10 hours per day. If the working time is longer due to production, the inspection and update of wearing parts, motors and other accessories should be strengthened to ensure the stability of the equipment.
- Product quality warranty for one year, (except for artificial or abnormal use) wearing parts are not included in the warranty scope. For details, please refer to the "wearing parts list" in the instruction manual.
- You are very welcome to visit our factory to see our machine how to work before you place an order with us.
- This product is delivered randomly: a manual and a set of molds (if other specifications are required, the cost will be quoted separately).
- If customer have any question about operation when using our machine,we will reply you by email/telephone/other online chat tool within 24 hours.
- The buyer needs to provide power voltage, compressed air gas source and grounding devices in accordance with electrical specifications on the site of the manufacturer's workshop; the buyer must configure the cables and air pipes connected to the equipment.
- The circulating cooling water, hydraulic oil (recommended to use 46 brand hydraulic oil), lubricating oil and cooling oil required by the equipment are purchased by the purchaser.